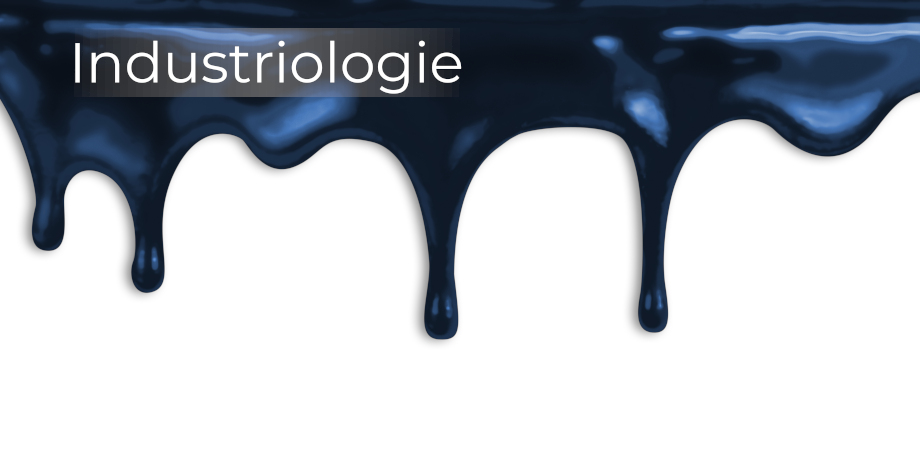
Qualité & Transformation de matière
Depuis près de dix ans, nous constatons les difficultés techniques systématiques d’industriels de la transformation de matière au sein d’organisations de toutes tailles, dans des secteurs pourtant aussi divers que la cosmétique, l’agroalimentaire, la pharmaceutique, les composites, les revêtements ou le traitement des déchets. Les facteurs d’influence de la conformité et des variabilités posent souvent des questions et le développement de produits nouveaux relève souvent du parcours du combattant.
Pourtant les méthodes pour la Qualité ne manquent pas et la plupart des acteurs concernés par ces difficultés ont des systèmes et démarches Qualité en vigueur. Comment s’expliquer alors que le développement ou l’industrialisation de produits nouveaux puissent être systématiquement si coûteux en temps et en ressources, avec un impact significatif sur les temps de mise sur le marché ?
Y’aurait-il différents niveaux de mise en œuvre de la démarche Qualité ? Certaines pratiques ne relèveraient-elles pas du périmètre de l’amélioration continue ? Les aspects techniques seraient-ils moins évidents à aborder que ne le suggèrent les manuels ?
Au fil des années, il nous est progressivement apparu nécessaire de chercher au cœur des méthodes qualité et de leurs présupposés les causes possibles de leurs propres limitations.
L’universalité de la Qualité
Originellement, la Qualité était centrée sur le Contrôle en production. Puis elle a progressivement élargi son champ d’action pour devenir une Démarche plaçant au centre la satisfaction des besoins clients et élargissant l’implication des différentes strates des organisations jusqu’à devenir un thème du Management, englobant toutes les dimensions de l’activité d’une organisation [1]. Certaines méthodes ont même pris le nom de Qualité Totale.
Chaque méthode, forte de ses succès -et probablement soucieuse d’élargir son champ d’application-, se présente souvent comme universelle, c’est-à-dire applicable à n’importe quel contexte industriel. Il est très difficile de trouver quelque mention explicite de possibles limitations -de la part de leurs promoteurs du moins… Au contraire, les échecs ou limites pratiques de mise en œuvre sont souvent imputés à une mauvaise compréhension des principes de la méthode ou à des freins dans leur mise en œuvre [2].
Pourtant, il ne semble pas déraisonnable d’estimer que toute analyse, théorie ou méthode s’applique dans un périmètre de validité qu’il est utile de chercher à définir pour en permettre une mise en œuvre optimale.
La stabilité du procédé
Sur le plan historique, les méthodes qualité sont essentiellement dérivées de la statistique, dont William Shewhart notamment a introduit et popularisé les méthodes au niveau industriel dans le cadre de son activité au sein des laboratoires Bell dans les années 1920 [3] [4].
Shewhart part du constat qu’un procédé de fabrication est inéluctablement soumis à des variabilités, plus ou moins importantes et contrôlables. Lorsque les variabilités laissent les attributs d’intérêt du produit à l’intérieur des intervalles de tolérance fixés, le procédé est considéré sous contrôle. A l’inverse, lorsque ces variabilités sont hors des limites de tolérance, le procédé est instable ; selon que ces variabilités sont chroniques ou sporadiques, le diagnostic est plus ou moins sévère sur l’instabilité du process. Shewhart associe la notion de cause à la notion de variabilités. Il définit la cause hasardeuse comme celle dont l’impact laisse le procédé dans sa zone de contrôle et la cause assignable comme celle qu’il s’agit d’identifier et d’éliminer [4].
Dans le contexte de la qualité en production, l’objectif est ainsi de préserver, et si possible d’améliorer, la stabilité du process. Le problème apparaît lorsque le process devient instable, par une déviance excessive de la qualité par rapport à l’intervalle de tolérance. L’histoire de la Qualité tout entière semble fondée sur ce principe.
L’instabilité du développement
Il existe pourtant un contexte dans lequel l’instabilité est non seulement inévitable, mais hautement nécessaire : le développement et l’industrialisation d’un produit nouveau. En effet, dès lors que les caractéristiques du produit visé sont suffisamment différentes des produits habituellement produits par une organisation, le process est par définition instable puisqu’il s’agit de le régler -dans certains cas même de le développer, voire de l’inventer- pour conférer au produit les caractéristiques requises.
Tous les secteurs de la formulation ou de la transformation de matière sont concernés : agroalimentaire, cosmétique, pharmaceutique, encre, revêtement, peinture, céramique, composite, pétrole, lubrifiants, …
Cette étape est par nature problématique, coûteuse en temps et en ressources, d’autant plus complexe dans les organisations à fort turn-over, avec un impact sérieux sur les temps de mise sur le marché. Le phénomène n’est pas plus une difficulté de PME que de grand compte.
Des facteurs communs aux causes communes
Le constat des similarités de difficultés entre organisations de secteurs pourtant variés n’est pas sans implication. Il suggère notamment que les causes communes de difficultés pourraient se situer au niveau de facteurs communs aux acteurs concernés. Citons-en quelques-uns.
Le premier des facteurs communs est lié à la nature des produits et activité concernés : des opérations liées au traitement et la transformation de matière, souvent ni complètement liquide, ni complètement solide à poudres, matières pâteuses, gel, émulsion, produits à changement de phase, etc.
Un deuxième facteur commun est que ces acteurs développent des produits ou procédés nouveaux. Il ne s’agit pas d’activité de fabrication mono-produit standardisée, mais au contraire de problématiques associées aux différentes étapes de la R&D à la mise sur le marché.
Un troisième facteur commun est que la plupart des acteurs procèdent dans ces étapes par la voie la plus traditionnelle qui soit : l’empirisme, c’est-à-dire par essai-erreur avec pour appui essentiel le savoir-faire disponible dans les équipes. Il s’agit donc de « faire », comme le cuisinier teste sa recette et ses variantes jusqu’à parvenir à un met à son goût.
Ainsi, dans ces phases instables, il ne s’agit pas de penser la résolution d’un problème ponctuel, mais plutôt les causes systémiques d’un faisceau de problèmes systématiques.
Sachant que les démarches Qualité usuelles ont pour la plupart ont été développées dans le contexte d’industries d’assemblage (téléphonie pour Shewhart ou Motorola, automobile pour Toyota, armement pour Crosby, …), il me semble utile d’inspecter si certaines traces des spécificités des activités de l’assemblage ne serait pas enfoui au cœur des méthodes, rendant ainsi leur transposition aux enjeux techniques de la transformation potentiellement problématique.
We planned it this way
Joseph Juran, un des grands noms de la Qualité, nous met sur la voie dès la préface de son célèbre Handbook of Quality : « Numerous specific quality crises and problems have been traced the way in which quality was planned in the first place. In a sense, we planned it this way » (De nombreux problèmes et crises spécifiques de qualité proviennent de la façon dont la qualité a été mise en place initialement. Dans une certaine mesure, nous l’avons organisée ainsi) [5].
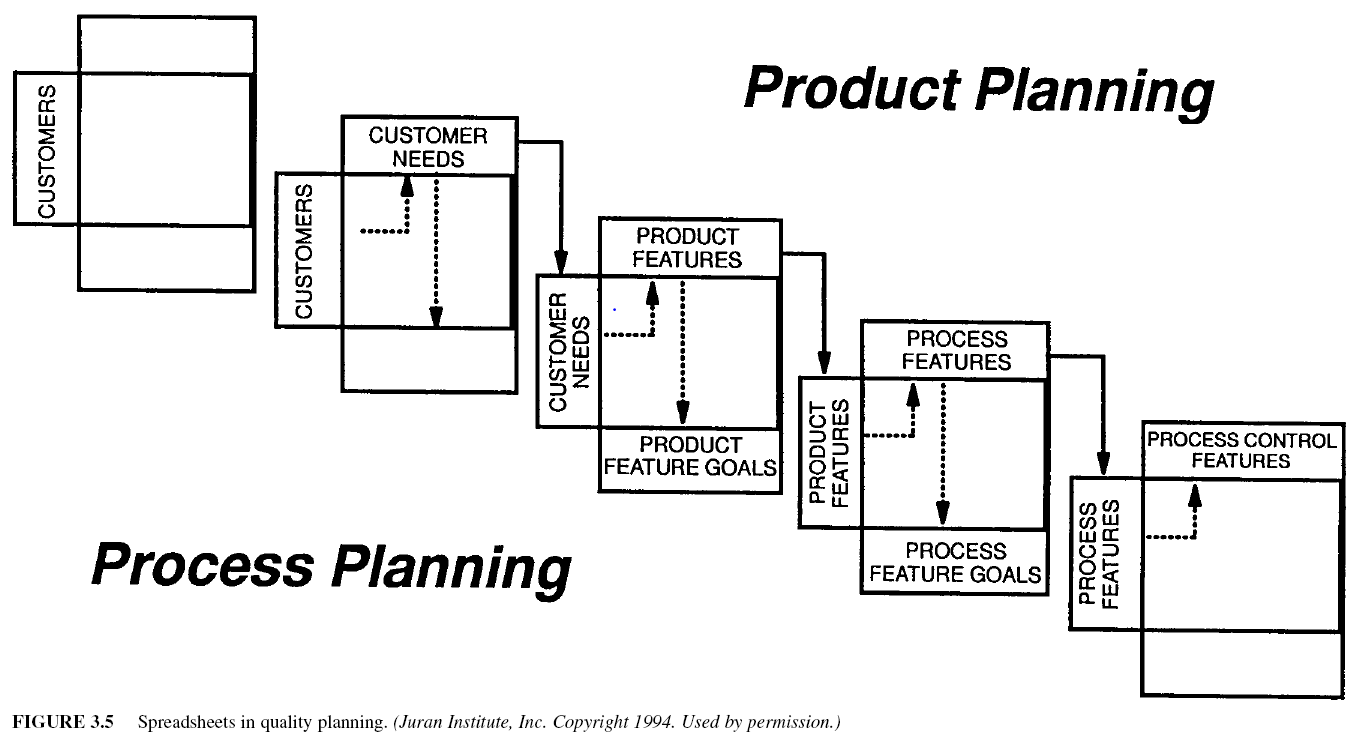
« Séquence universelle du Planning Qualité » d’après Juran, issu de [5]
Si l’on s’intéresse à la démarche proposée par Juran, on constate que celui-ci définit une « séquence universelle du planning qualité », illustrée dans la figure ci-dessus. Dans cette démarche, sur le plan technique, il s’agit de designer le produit puis le process qui permettra de le fabriquer effectivement. Pour atteindre un process sous contrôle, la logique de stabilité demande de fixer les conditions liées d’une part à la matière, d’autre part au process.
Séquence vs Réalité
Or, si la logique d’une telle séquence semble implacable, sa mise en œuvre pour les enjeux techniques de transformation de matière est loin d’être complètement triviale. En effet, le design et la faisabilité du produit en projet – une nouvelle émulsion crème, un nouveau dessert, un nouveau composite, une nouvelle graisse, …- nécessite une première réalisation concrète. C’est la mission de la R&D.
Il s’agit de transformer des ingrédients par le biais des procédés pour en faire un produit aux caractéristiques spécifiques. Dans ces transformations, matière et procédé sont aussi déterminants l’un que l’autre : changez les matières, le produit change ; changez votre procédé, ou ne serait-ce que l’ordre d’incorporation, le produit est susceptible de changer aussi. L’analogie culinaire est toujours éclairante sur ces questions. Imaginez préparer une vinaigrette et pensez à l’impact sur la texture de l’émulsion de la vitesse à laquelle vous remuez cuillère ou fourchette.
Dans l’étape suivante, lorsqu’une version satisfaisante du produit est obtenue à l’échelle laboratoire -c’est-à-dire avec certains moyens de préparation-, le recours à d’autres moyens pour une fabrication à une échelle supérieure ne va pas de soi. En clair, il ne s’agit pas d’assembler des pièces indépendantes ; produit et process sont fortement couplés. C’est une particularité de ces systèmes dits complexes, qui fait aussi leur richesse d’application.
Le plus souvent, les produits sont composés de plusieurs ingrédients (souvent entre 5 et 40), pour lesquels il est absolument impossible à partir des propriétés indépendantes des ingrédients d’en déduire celles du produit fini. Ainsi, en l’absence d’outils de conception assistée par ordinateur utilisés dans la grande majorité des industries mécaniques et d’assemblage, le recours aux approches empiriques semble être la seule approche -nous verrons cependant lorsque nous présenterons notre propre méthodologie que des approches alternatives plus efficaces peuvent être développées.
La mesure : indispensable mais invisible
Un élément supplémentaire d’analyse concerne la mesure, dont Juran indique dans le commentaire de la séquence universelle qu’elle concerne toutes les étapes. Mais de quelle mesure s’agit-il ? Dans son ouvrage, et la plupart des auteurs font de même, Juran fait principalement référence à la mesure par capteur, c’est-à-dire la mesure de propriétés « simples ».
Dans la transformation de matière, les propriétés simples sont souvent insuffisantes. Les propriétés des entrants comme des produits finis ne donnent aucune information sur les états intermédiaires pourtant cruciaux dans les étapes de transformation de matière.
Au contraire, les mesures telles qu’usuellement pratiquées dans le domaine de la transformation de matière tendent même à considérer identiques des ingrédients ou des produits dont les différences sont propres à occasionner des variations notables en process comme en application.
J’ai eu l’occasion d’aborder ces questions autour des notions de viscosité dans des articles précédents ; le comportement des poudres par exemple pourrait faire l’objet d’une démonstration équivalente. Sur ces aspects, les connaissances scientifiques ont largement évolué, bien plus rapidement que les standards de mesure.
Il est d’ailleurs à noter que dans toutes approche fondée sur la statistique, la mesure est un présupposé, puisque c’est d’elle que proviennent les données. Aucun traitement pertinent avec des mesures erronées ou évasives -en particulier celles qui peinent à distinguer deux produits dont les comportements sont en pratique différents. Ce point est crucial et pourtant très peu interrogé dans les manuels méthodologiques.
La mesure est absolument indispensable, mais elle devient invisible dès lors qu’il s’agit de traiter des données.
L’incompréhension des phénomènes, une cause racine de difficulté ?
Ainsi, les questions de développement et d’industrialisation de produit et procédé nouveaux dans les secteurs de la transformation de matière posent certaines questions sur le périmètre d’application des démarches Qualité usuelles pour les questions techniques.
Dans ces étapes d’instabilité, aucune réalité statistique ne permet de guider l’action, si bien que les acteurs se retrouvent souvent contraints à procéder par empirisme. En pratique, il ressort que la compréhension des phénomènes à l’origine des variabilités observées est difficile à acquérir.
A bien y regarder d’ailleurs, la plupart des méthodes Qualité considère une telle compréhension soit comme allant de soi, soit comme le fruit des démarches notamment statistiques. Il est assez étonnant de constater dans la plupart des manuels l’absence complète de cette notion de compréhension.
Pourtant, depuis plusieurs décennies maintenant, un autre grand nom de la Qualité, W. Edward Deming, insiste sur la nécessité d’un « profound knowledge » qui passe notamment par la compréhension des variations et plus généralement de la systémie de l’organisation [6]. Depuis quelques années, la Food and Drug Administration promeut la méthode du Quality by Design qui présente la particularité d’insister sur la nécessité d’un prior knowledge.
Citons d’ailleurs un ouvrage récent de Quality by Design pour la pharmaceutique, qui en introduction décrit une situation qui dépasse à mes yeux largement le cadre de la pharmaceutique : « Historically, an ultra-compliant approach had dominated the way the pharmaceutical industry operated, perhaps even threatening, wrongly, to potentially swamp the underlying science, rather than compliance being seen as a partnership with science.” [7] (Historiquement, une approche extrême de la conformité a dominé les pratiques pharmaceutiques, probablement même au détriment de la science sous-jacente, plutôt qu’en établissant une complémentarité avec la science.)
Une telle complémentarité est certainement un atout majeur dans un monde où l’agilité devient un facteur majeur de compétitivité.
Références
[1] C. Yang, The Evolution of Quality Concept and the related Quality Management, 2017, Intech
[2] G. Barouch S. Kleinhans , Learning from criticisms of quality management », 2015,
International Journal of Quality and Service Sciences, Vol. 7 Iss 2/3 pp. 201 – 216,
[3] D. Bayart, La quantification du contrôle qualité dans l’industrie : un point de vue sociologique et historique. In: Économie rurale. N°217, 1993. La qualité dans l’agro-alimentaire. pp. 18-23
[4] W. A. Shewhart, Economic control quality of manufactured product, 1931, D. Van Nostrand Company
[5] J. Juran, Juran’s Quality Handbook, 5th ed., 1999 (1st éd. 1951), McGraw-Hill Companies Inc.
[6] W. Edwards Deming, The New Economics for Industry, Government, Education, 1994, MIT Press
[7] W. Schlindwein & M. Gibson (editors), Pharmaceutical Quality by Design A Practical Approach, 2018, John Wiley & Sons Ltd
Last Updated on 15 septembre 2022 by Vincent Billot