Introduction to Behavioral Instrumental Techniques
The processing industries materials are full of measuring instruments and standards intended to quantify macroscopic properties related to the flow, texture or mechanical strength of ingredients, finished or semi-finished products.
Among them, sections of viscosity, Hall funnel, viscometer, texturometer, rheometer, tribometer, durometer and other DMA, are instruments intended to assign values to macroscopic behaviors of different types of matter (powders, fluids, pasty, semi-solids, …).
Often used both in quality control and in R&D, these instruments often pose difficulties: the measurements struggle to differentiate materials or products that differ in their actual behavior. Thus, without reliable ability to discriminate, the measurement is then reduced to producing a control value of little interest.
In this article, we briefly present these techniques and their operating principles, thus offering an unprecedented analysis grid of their possible uses and their limits.
Empirical instrumental techniques by gravity flow
The most rudimentary of the rheological measurement techniques aim to quantify the flow of matter under the effect of its own weight, by gravity.
Depending on the geometry and the principle of the device, a flow time, a distance travelled, a characteristic orifice size, an angle, will be measured, which will give an indication of a tendency for the product to flow. We often talk about viscosity index for fluids, flowability for powders, consistency for pasty products.
Viscosity cup
The viscosity cup (which historically was the first device called a “viscometer”) has the shape of a funnel through which a sufficiently fluid product can flow. The flow time of a given quantity of fluid is measured. Generally, the dimensions and characteristics of the cut are standardized (Ford cut, Zehn cut, etc.).
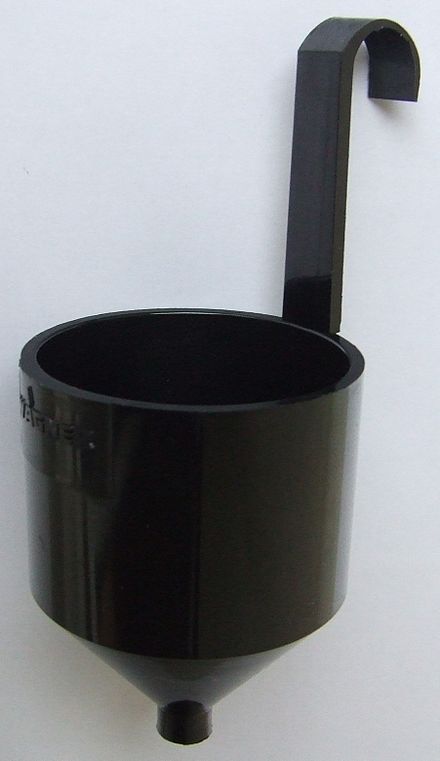
On this principle, there are also efflux viscometers, devices of the viscosity cup type equipped with temperature control means (see our article A brief history of viscometry and rheometry).
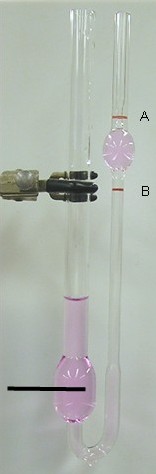
Capillary viscometer
The capillary viscometer was popularized by Ostwald in the second half of the XNUMXth century. Consisting of a U-shaped tube, it makes it possible, by measuring the passage time of a fluid between two marks, to determine a viscosity index.
The capillary viscometer is still in standard use for Newtonian products in certain fields (for oils in particular).
Flowability of powders: Hall/Carney funnel flow meter, Flodex, slope angle
For powders, there are various flow devices through a standardized funnel-type geometry device. We often talk about flowability measurements.
The Hall funnel flowmeter operates on a principle equivalent to the viscosity cup: the flow time of a given volume of powder through the device is measured.
The Flodex is based on a funnel device with a slightly different quantification principle: it involves determining the diameter of the minimum orifice allowing the powder to flow. For this, it is a question of repeating the flow experiment with orifices of progressively decreasing sizes. The diameter of the orifice is associated with a flowability index.
Finally, slope angle measurement is also based on the use of a funnel-type device to prepare a pile of powders. The slope angle of the pile is then measured either by goniometric or optical means.
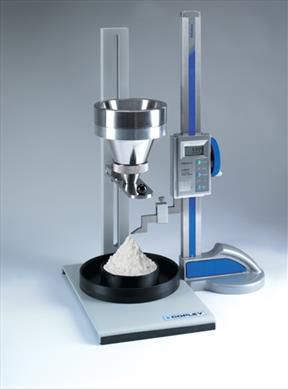
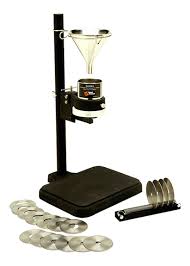
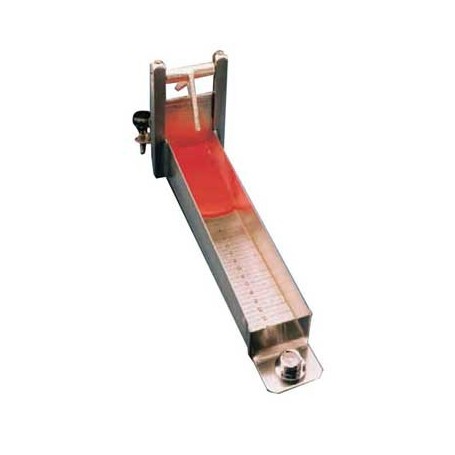
Bostwick Consistometer
The Bostwick consistometer is a standardized inclined plane type device dedicated to rather pasty products. The product, deposited at the top of the inclined plane, gradually spreads out along the plane under the effect of its weight. The distance traveled gives a numerical value associated with the consistency of the product.
Progress point: empirical techniques measuring purely operational quantities
In these various techniques, often described as empirical, the quantities measured are generally not defined scientifically, but essentially operational : the quantity measured is defined exclusively by what the device quantifies through its own mode of operation, without any particular relationship to a property established on the theoretical level.
For example, the consistency measured with the Bostwick consistometer combines at least contributions linked to the density of the product (conditioning the effect of gravity), to its rheology (more or less flow threshold) and its physics at the interfaces (more or less sticky or slippery products will flow very differently). Thus, very different products will be likely to have equivalent consistencies. However, for products with similar formulations, the differences in measured consistency will constitute an indicator of their difference.
Another example, the flow time of a product measured during its passage through a viscosity cup presents an arithmetic relationship with the viscosity of the fluid only in the particular case of Newtonian fluids (see our article Viscosity, rheology and confusion). In the case of fluids exhibiting more complex rheologies (non-Newtonian, threshold, etc.), the flow time, although capable of operationally reflecting a tendency relating to flowability, cannot constitute a measurement of viscosity.
Instrumental techniques with mechanical constraints
In contrast to these techniques based on a quantification of behavior under the effect of gravity, there are instrumental techniques based on theapplication controlled mechanical constraints: instrumental techniques with mechanical constraints.
Instrumental techniques with mechanical constraints are likely to exploit the different modes of stresses and deformations of matter known at the macroscopic scale: compression, traction, torsion, bending, shear.
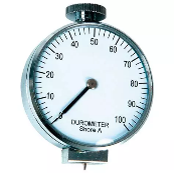
Durometer
The durometer is a technique for measuring hardness, dating from the 1920s, based on the application of a stress of compression on a restricted surface (indentation), using an indenter of standardized constitution and dimensions (adapted according to the nature of the product to be measured).
The durometer quantifies the force necessary for a defined indentation, in different hardness scales (Shore, Rockwell, Vickers, Brinell) suitable for testing different types of materials (elastomers, plastics, metals, leather, wood, etc.).
There are also durometers and associated standards for brittle or thin materials (Knoop test).
Viscometer
The viscometer, which appeared at the beginning of the XNUMXth century, applies to the product a constraint of shear by rotation of a mobile (of variable geometry according to the models and nature of the products) in a container containing the product and quantifies the modification of the engine torque caused by the presence of the product, translated into a viscosity value.
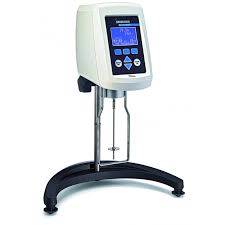
In practice, particularly in the case of Brookfield viscometers, the most common, the measurement is carried out with a spindle whose speed of rotation is fixed (in rpm, round-per-minute, i.e. in revolutions-per-minute). -minutes), coupled with a temperature measurement.
Viscometers are dedicated to rather fluid products, with certain limitations depending on the specific properties of the product (see our article Viscosity, rheology and confusion).
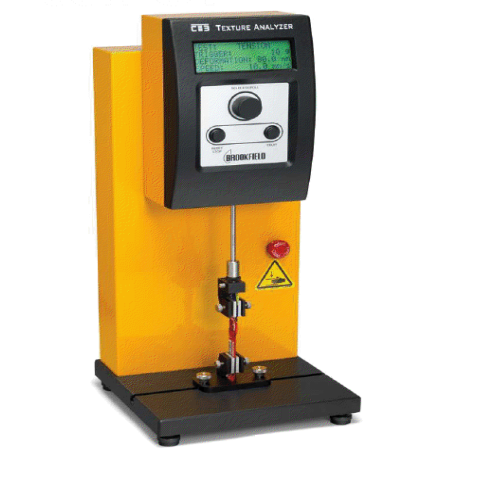
Gelometer
The gelometer is intended to quantify certain properties of gels and, by extension, of phase change products. This device exists in two variants: one oriented towards the measurement of force of gel, operating in compression, a gel time quantification oriented, operating in shear.
Compression gelometers are variants of the Bloom tester, developed in the 1920s for gels and gelatins, and similar to the operating principle of the durometer. This involves determining the penetration limit mass of a standardized plunger causing a certain deformation of the gel without rupture; this weight is translated into a gel strength/consistency in Bloom units. Contemporary versions rather determine a limit force before rupture.
Shear gelometers operate on the principle of a viscometer with a mobile hook whose rotation is progressively prevented by the gelation or setting of the product. Kinetic monitoring makes it possible to determine a freezing time.
Texturometer
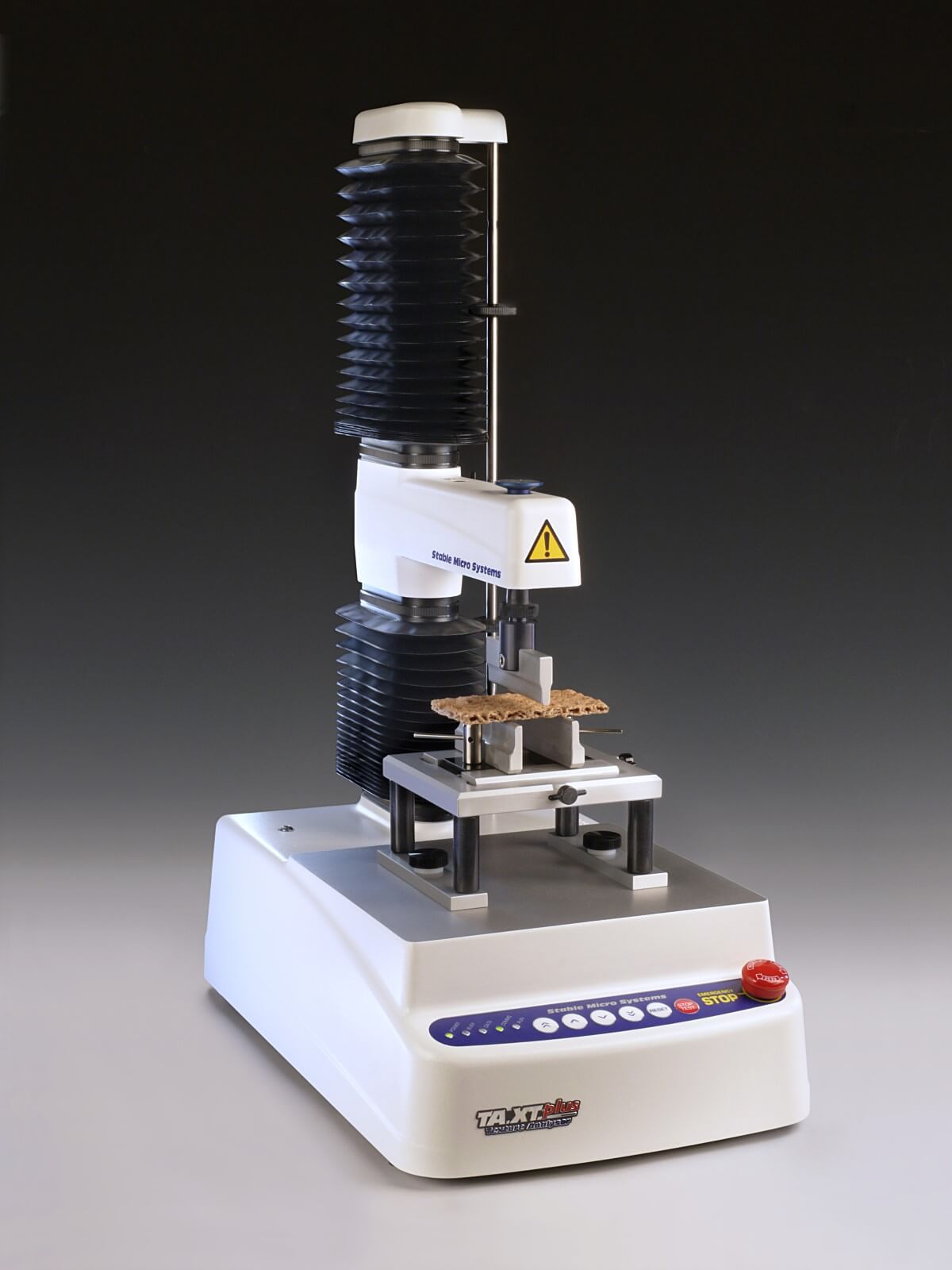
The texturometer, initially developed in the 1960s for the needs of the food industry on the basis of the little-known denture tendrometer, operates on a principle of stresses of compression on textured products.
The usual approach of Texture Profile Analysis (TPA) consists in imposing deformation cycles and exploiting the force response (and its integrals) induced by the product to be tested, making it possible to trace back to independent parameters of hardness, stickiness, cohesiveness, elasticity and delicate translation parameters in French: brittleness, chewiness, guminess.
More exotic approaches use different mobiles and test benches adaptable to the texturometer to impose stresses according to more specific configurations, from slight deformation to the penetration of the mobile, the slicing of the product, its bending, its rupture (for example in the case of crunchy products).
The texturometer translates well this notion of behavioral instrumental technique, in which it is a question of reproducing macroscopic constraints by the methods of implementation of an instrumentation with the principles of robust mechanical operation on the scientific level. The protocol configuration options, which vary according to the models, open up many ways of behavioral quantification.
Dynamic Mechanical Analysis
DMA is a technique for measuring the viscoelastic properties of materials. Based on the application of compression constraints, the DMA exploits a particular mode of application that we will find in the rheometer: oscillations. The compression oscillations are applied at a given frequency and amplitude (under given thermal conditions). The responses of the materials (in phase and in phase opposition) make it possible to trace the viscoelastic moduli (in compression) E' and E''.
Applying "sweeps" (sweep) in frequency and/or amplitude and/or in temperature makes it possible to determine various dynamic behavior parameters, in particular the phase transition temperatures (glass transition in particular for polymers).
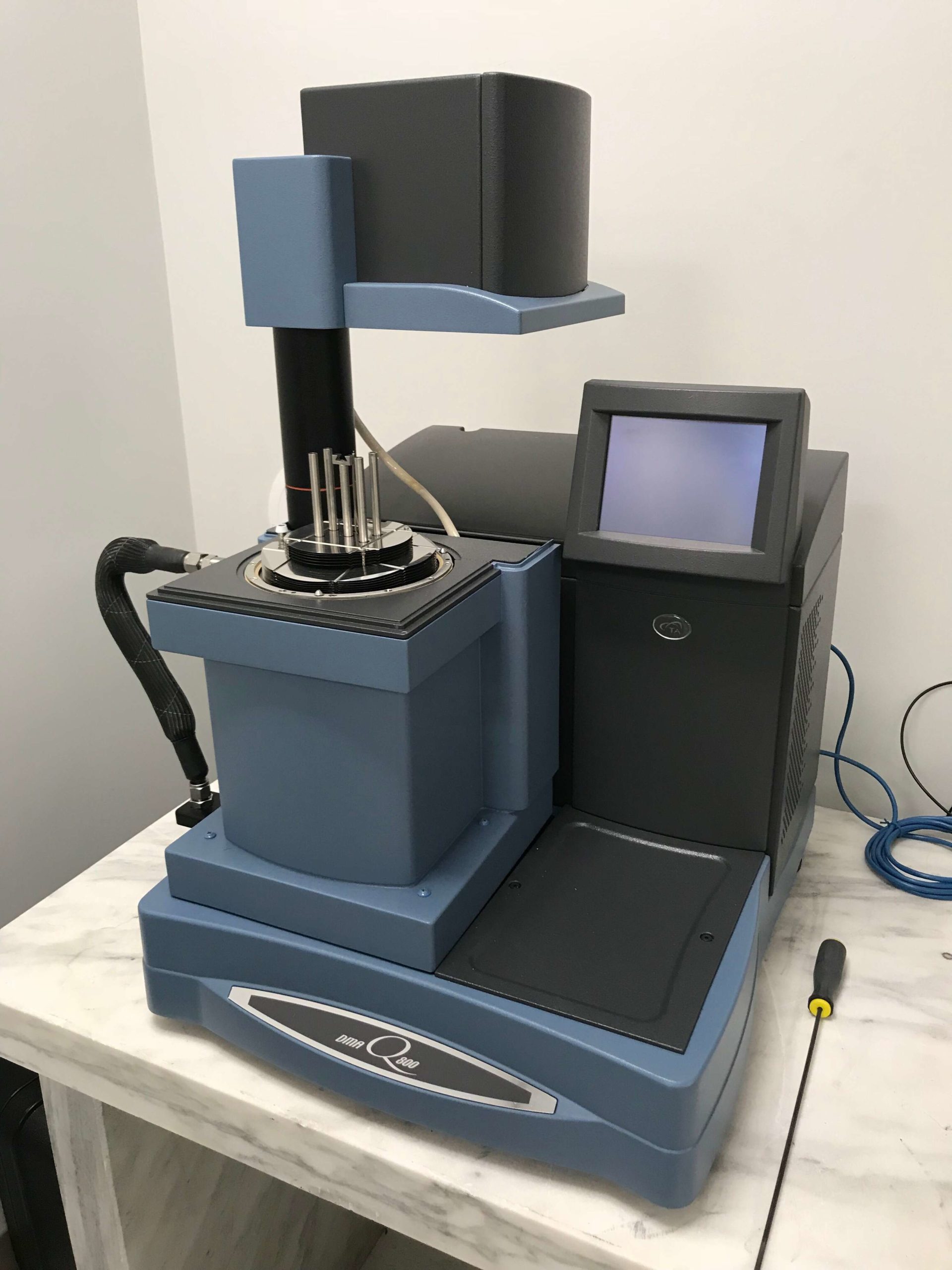
Mainly used in the field of polymers, DMA is of interest in principle for all types of flexible or phase-change materials.
Tribometer and tribotesters
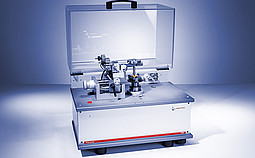
The tribometer is an instrumentation dedicated to determining the tribological properties, that is to say the properties of friction, wear and lubrication between two materials. This instrumentation, invented in the 18th century, thus applies stresses combining compression and shear.
Like texturometers, tribometers are often equipped with modules allowing constraints to be applied according to movements (and within ranges of effort) characteristic of the application context to be simulated: four-balls, ball-on-disc , ball-on-three-plates, ring-on-ring, discs, …
Rheometer
Developed in the 1970s, and constantly improved since, the rheometer is certainly the most versatile instrument of behavioral instrumentation, in that it has the particularity of being able to impose mechanical constraints of any type (shear, compression, extension, bending, twisting).
The rheometer is thus both a viscometer (in principle) perfected, a texturometer, a DMA, a tribometer*. Depending on the range, you will find instrumentation with various performances, more or less configurable.
In general, it seems possible to identify four main modes of use of the rheometer:
- Rheometry conventional, dedicated to the measurement of rheological properties in flow (viscosity, yield stress, thixotropy, etc.)
- Advanced rheometry, applying the oscillating stress mode, in shear for the viscoelastic measurement of G', G'' - and in compression, only accessible on certain ranges.
- Exotic rheometry, exploiting compression modes of the texturometry type or hybrid compression/shear of the tribometry type
As for the texturometer or the tribometer, many specific cells make it possible to impose constraints in particular configurations and to extract semi-empirical quantities (less robust than properties based on complete theories, but more scientific than related parameters stress modes exciting several types of phenomena).
Note also the existence of specific rheometers: Extensional rheometer (often called by the name of its main commercial model: the Caber), capillary rheometer, exotic rheometer, instrumented micro-pilot.
conclusions
At the end of this non-exhaustive overview of common instrumental techniques in the processing industries, it is possible to draw up an initial assessment:
- Far from being reduced to measuring a quantity (as one would do with a ruler or a tape measure to measure a distance), behavioral instrumental techniques impose mechanical constraints on matter in order to determine reactions (responses) of matter in return.
- These stresses are imposed at the macroscopic scale by gravity flow, compression, shear, extension, bending or torsion. Environmental constraints (temperature in particular) can also be controlled.
- These constraints are more or less configurable according to the instrumentations, limiting the determination of response to single values or sets of points (function) according to the imposed constraints. Thus, the variety of possible stress modes multiplies the types of responses, physical, mechanical, rheological, tribological, texture, etc.
- The nature of the states of matter depends on the type of device and the possible parameterization conditions of the stresses to be applied.
These considerations on instrumental techniques should not make us forget that any measurement is underpinned by a context of questioning. Often, the views focused on measurement disregard the questions that motivate it, as if the quantity to be measured to answer such and such a question was self-evident. This is not the case, in particular for industrial issues, and the variety of instruments mentioned constitutes concrete proof of this.
You wish to discuss with our team of specialists your instrumentation questions and their use
Last Updated on November 4, 2022 by Vincent Billot